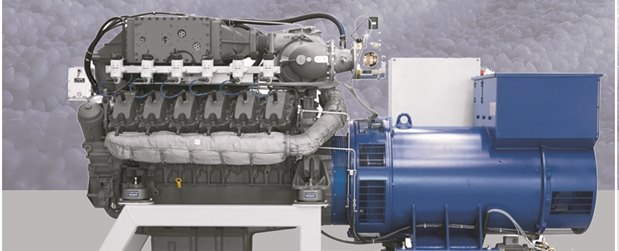
Interview with Peter Breuer, Group Trainings and Innovation Management at motan holding GmbH. Based in Konstanz on Lake Constance, the company develops raw and other materials handling systems for the plastics manufacturing and processing industry.
What are the implications of functional integration for motan?
Peter Breuer: For us as a peripherals manufacturer, functional integration means that ever greater demands are made of control systems and interfaces. We constantly have to adapt. We also have to become more and more involved with the customer's complex systems as a whole. In the past we might have sold a dosing device, for example, without needing to know precisely where and how the customer used it. That has changed radically. Now we have to be familiar with the entire system of the manufacturing process, including aspects that are not really our concern as equipment manufacturers, so that we can take the right decisions for the specific application.
Why is it no longer enough just to sell equipment?
Breuer: Take energy as an example. If we want to use combined heat and power (CHP), which is very efficient in terms of energy use, to heat a drying bin, we have to make an energy analysis of the entire production system. Only then can we decide which energy flows should sensibly be disconnected from a block-type thermal power station and where – apart from heating the drying bin – they can still be used. Motan equipment has to interact with other devices that are not made by motan but are connected to it as part of the system.
Do you also integrate functions into your own equipment?
Breuer: In general terms, a measure of functional integration has been the state of the art in our equipment for a number of years now. We are in fact already well advanced there. In the past, integration has for example meant that a dryer's control system also has the function of driving a conveyor. The same goes for mixers and dosers. Now we have to leave that level of integration behind and broaden our perspective. We have to be able to interlink with all the surrounding system. This can extend as far as production logistics and operational structures.
Who is driving this development? The end user or motan?
Breuer: The initial impulse generally comes from the end users. They have specific requirements, or even just an idea, that they put to us. We take up that idea and develop it further until a product innovation emerges at the end. We have always been very much geared to application technology.
What predominates with functional integration, the opportunities or the risks?
Breuer: The opportunities predominate, otherwise nobody would bother with functional integration. Functional integration makes for greater cost-effectiveness and greater efficiency. It also allows plant and machinery to be simplified and made easier to operate and improves the transparency of data. We have reached a point where developments in consumer electronics are increasingly finding their way into industry. In the future, I will be able to start and control a process via my material handling system using my smart phone, provided I have the right interfaces. This is still some way off, but it is a trend people are working on and it will be here in a few years' time. Internet technology will continue to spread. It is one of the driving forces of functional integration. Others are energy management and product individualisation.
Does the Internet not present a risk? After all, data can be stolen or manipulated in the cloud.
Breuer: There is still much to be done here. But security becomes an issue far earlier than that: with the use of viruses to seize production data. All PCs now run a virus scanner, but that is still far from being standard practice with automation systems. A lot of systems are therefore vulnerable. In my opinion a lot of IT basics still have to be developed here before the level of security in industry is significantly improved.
What other risks are there?
Breuer: Increasing functional integration is making processes more complex. We have to take care not to lose control of them. The more we integrate and the more control is required, the more complex machines become. We should not take it too far. There also needs to be a sensible relationship between the benefits of functional integration and the overall cost.
How sustainable is functional integration?
Breuer: Sustainability is not an end in itself. In the first instance, it is always about increasing efficiency and cost-effectiveness in the use of resources. Nowadays that often means that we concern ourselves primarily with energy balances. Because energy is getting increasingly expensive. Our design for combined cooling, heating and power generation (CCHP) for example optimises overall energy efficiency between the primary energy input and the energy used in production. But even with this optimisation, primary energy is still needed, most of which comes from non-sustainable sources such as natural gas. If we are to achieve genuine sustainability, we must now in a next step switch to a renewable energy source such as biogas. The CCHP technology we use with a block-type thermal power station will encourage this.
The motan Group
based in Konstanz on Lake Constance was founded in 1947. Its applications-oriented range of products includes modular systems for the storage, drying and crystallising, conveying, dosing and mixing of raw materials for the plastics manufacturing and processing industry. Made at various locations in Germany, India and China, its products are sold all over the world. With a workforce of more than 450, the Group currently has annual sales of some 110 million euro.
Sustainability is one of today's big issues. Dwindling resources and a growing world population make it unavoidable. That is why the VDMA launched the Blue Competence sustainability initiative. More than 400 firms have joined the network since it started three years ago. 55 of them are members of the Plastics and Rubber Machinery Association. That makes the industry a trailblazer among German plant and machinery manufacturers when it comes to environmental protection, conservation of resources and management efficiency.
Sustainability has many facets. These include both greater efficiency in the use of energy and resources, better training and good corporate management. Functional integration, the concentration of different tasks in one component or production process, is also part of it. In the run up to FAKUMA the VDMA is presenting a series of interviews on this topic.
www.vdma.org